Panneaux solaires à base de biomatériaux – PV India Magazine
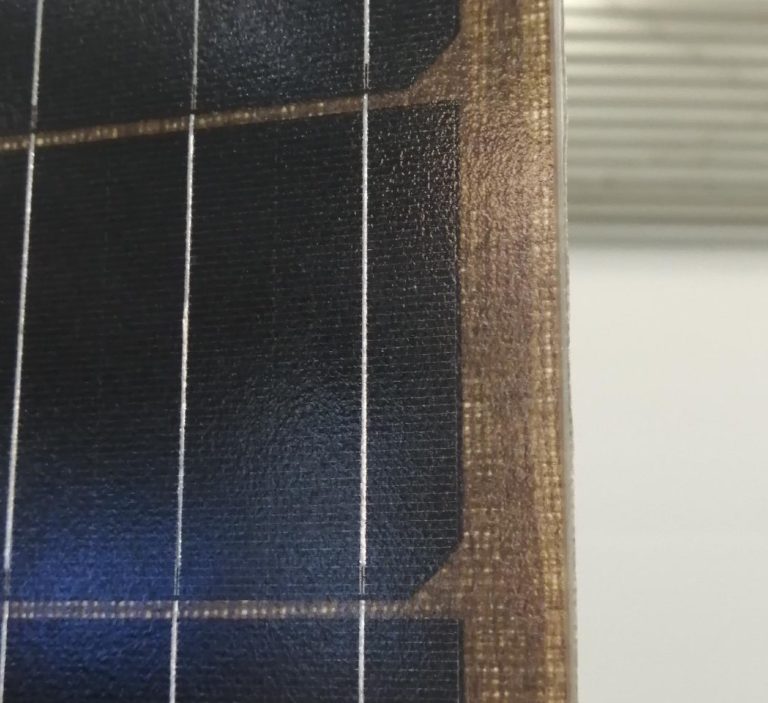
L’Institut français de l’énergie solaire INES a développé de nouveaux modules photovoltaïques à partir de thermoplastiques et de fibres naturelles d’origine européenne, comme le lin et le basalte. Les scientifiques visent à réduire l’empreinte environnementale et le poids des panneaux solaires, tout en améliorant le recyclage.
De Magazine du monde du photovoltaïque
Chercheurs en France Institut National de l’Energie Solaire (INES) – section de Commissariat aux Energies Alternatives et à l’Energie Atomique (CEA) Nous développons des modules solaires intégrant de nouveaux biomatériaux sur les faces avant et arrière.
« L’empreinte carbone et l’analyse du cycle de vie devenant désormais deux critères principaux dans le choix des panneaux photovoltaïques, les économies de matière deviendront un élément critique en Europe dans les prochaines années », a déclaré Anis Foeny, directeur du CEA-INES. , dans un entretien avec PV France.
Aude Derrier, la coordinatrice du projet de recherche, a déclaré que ses collègues se sont penchés sur divers matériaux déjà en place, pour trouver un matériau qui pourrait permettre aux fabricants d’unités de produire des panneaux qui améliorent les performances, la durabilité et le coût, tout en réduisant l’impact environnemental. Le premier démonstrateur est constitué de cellules solaires hétérogènes (HTJ) noyées dans un matériau entièrement composite.
« La face avant est faite d’un polymère chargé de fibre de verre, ce qui assure la transparence », a déclaré Derer. « La face arrière est constituée d’un composite à base de thermoplastique dans lequel ont été incorporés des tissages de fibres de lin et de basalte, apportant une résistance mécanique, mais aussi une meilleure résistance à l’humidité. »
Le lin provient du nord de la France, où se trouve déjà tout un écosystème industriel. Le basalte provient d’ailleurs en Europe et est filé par un partenaire industriel de l’INES. Cela a permis de réduire l’empreinte carbone de 75 grammes de CO2 par watt, par rapport à une unité de référence de même puissance. Le poids a également été amélioré et est désormais inférieur à 5 kg par mètre carré.
« Cette unité est destinée à l’intégration de bâtiments photovoltaïques sur le toit », a déclaré Derer. « L’avantage, c’est qu’il est naturellement de couleur noire, sans qu’il soit nécessaire d’avoir une coque arrière. En termes de recyclage, grâce aux thermoplastiques, qui peuvent être refondus, la séparation des couches est aussi techniquement plus simple. »
L’unité peut être réalisée sans adaptation des procédés existants. L’idée, a déclaré Derer, est de transférer la technologie aux fabricants sans investissement supplémentaire.
« La seule chose est d’avoir des congélateurs pour stocker le matériau et non pour démarrer le processus de réticulation de la résine, mais la plupart des fabricants utilisent aujourd’hui le pré-durcissement et sont déjà équipés pour cela », a-t-elle déclaré.
Les scientifiques de l’INES se sont également penchés sur les problèmes d’approvisionnement en verre solaire rencontrés par tous les opérateurs photovoltaïques et ont travaillé à la réutilisation du verre trempé.
« Nous avons travaillé sur Second Life Glass et développé une unité en verre recyclé de 2,8 mm provenant d’une ancienne unité », a déclaré Dererer. « Nous avons également utilisé une pellicule thermoplastique qui ne nécessite pas de réticulation, donc facile à recycler, et un composé thermoplastique avec des fibres de lin pour la résistance. »
La face arrière sans basalte du module a une couleur de lin naturel, ce qui pourrait être esthétiquement agréable pour les architectes en termes d’intégration de façade, par exemple. De plus, l’outil de calcul INES a montré une réduction de 10 % de l’empreinte carbone.
« Il faut maintenant remettre en question les chaînes d’approvisionnement photovoltaïques », a déclaré Al-Juwayni. « Avec l’aide de Rhône-Alpes dans le cadre du plan de développement international, nous sommes allés chercher des acteurs extérieurs à la filière solaire pour trouver de nouveaux thermoplastiques et fibres. Nous avons également réfléchi au procédé de laminage actuel, qui nécessite beaucoup d’énergie. »
Entre la phase de pressage, de pressage et de refroidissement, le laminage dure généralement entre 30 et 35 minutes, avec une température de fonctionnement allant de 150°C à 160°C.
« Mais pour les appareils qui intègrent de plus en plus des matériaux éco-conçus, il faut convertir les thermoplastiques autour de 200°C à 250°C, sachant que la technologie HTJ est sensible à la chaleur et ne doit pas dépasser 200°C », précise Derrier.
L’institut de recherche collabore avec le spécialiste français des presses à induction à chaud, Roctool, pour réduire les temps de cycle et réaliser des formes selon les besoins des clients. Ensemble, ils ont développé un ensemble dont la face arrière est constituée d’un composé thermoplastique de type polypropylène, dans lequel ont été incorporées des fibres de carbone recyclées. La face avant est en thermoplastique et en fibre de verre.
« Le processus de presse à chaud inductif de Roctool permet de chauffer rapidement les plaques avant et arrière, sans avoir à atteindre 200°C au cœur des cellules HTJ », a déclaré Dererer.
L’entreprise affirme que l’investissement est moindre et que le processus peut atteindre un temps de cycle de quelques minutes seulement, tout en utilisant moins d’énergie. Cette technologie s’adresse aux constructeurs automobiles, pour leur donner la possibilité de produire des pièces de formes et de tailles différentes, tout en incorporant des matériaux plus légers et plus durables.
Ce contenu est protégé par le droit d’auteur et ne peut être réutilisé. Si vous souhaitez coopérer avec nous et souhaitez réutiliser certains de nos contenus, veuillez contacter : editors@pv-magazine.com.